Seafood leadership training strengthens industry
May 7, 2018
Sue Keller
907-474-6703
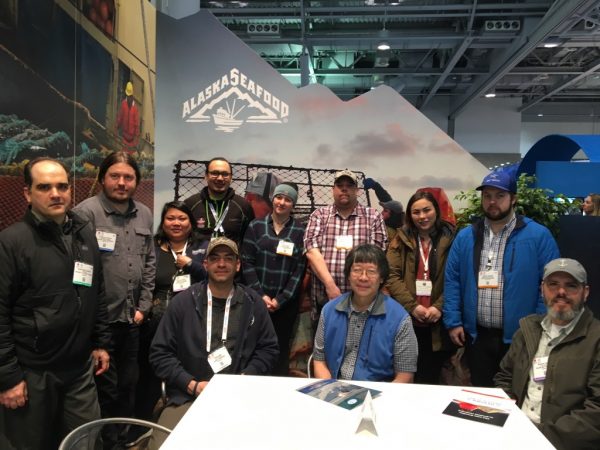
Learning to lead effectively is key for employees who want to advance in their companies. Alaska Sea Grant has trained nearly 100 midlevel managers over the past 10 years at the Alaska Seafood Processing Leadership Institute to ensure the industry grows and remains strong.
“The 2018 graduates overall seemed exceptionally motivated, energetic and eager to participate in the series of topics presented,” said Quentin Fong, Alaska Sea Grant seafood marketing specialist. Fong is lead organizer for the course.
Eighteen students completed a week of training each in November 2017 and March 2018, they worked on a plant project during the intervening months, and ten students attended the International Seafood Expo in Boston.
Sam Nothstine, expediter at Kwik’pak Fisheries in Emmonak, Alaska, said the most useful part of the training was the session taught by independent leadership trainer Al Bolea. Nothstine learned from Bolea’s first-hand stories about how he became CEO in the oil industry and the decisions he made on the job.
“He encouraged us to be communicative and challenge others, not to retreat from issues,” said Nothstine.
“But the most important aspect of ASPLI is the mentors, especially Chris Sannito and Quentin Fong,” said Nothstine. “They had a very close connection with the students. They encourage everyone to reach their potential, and they are continuing to offer help which I really appreciate.”
Fong and Sannito, both faculty members in the College of Fisheries and Ocean Sciences, taught seafood business and processing during the November session at the Kodiak Seafood and Marine Science Center and at the March session in Anchorage, along with other experts. They also offered guidance on the projects.
Student projects ranged from adopting lean manufacturing principles in plant operations and enhancing processor ergonomics, to creating mobile work stations and redesigning offloading operations. They gave presentations on the projects during the March class.
“My project was to do an equipment inventory and learn the purchasing process. We went from two refrigeration units to four, and bought some new engines that had given us problems,” said Nothstine.
When Nothstine gave his presentation he also showed a video of his grandfather, Jake Johnson Sr., who in the 1970s started the fish processing cooperative that became Kwik’pak Fisheries. Kwik’pak is the only employee-owned and Native-operated seafood processor in Alaska.
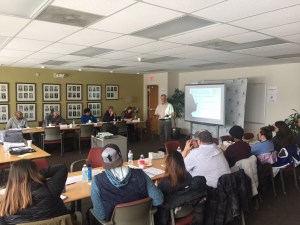
According to Fong the Alaska Seafood Processing Leadership institute has really taken off after its 10 years of existence, and people in the seafood industry are much more aware of its value. “About half the participants heard about it from their coworkers or acquaintances and asked their boss if they could take the class,” he said.
Nothstine, however, was nominated by his company. Kris Norosz, a member of the Alaska Sea Grant Advisory Committee, contacted Kwik’pak looking for potential leaders who might benefit from ASPLI training. “Two separate people gave her my name,” he said.
After taking the course Nothstine is doing very well. “Management here has taken advantage of my new mindset and skills, and I’m implementing new ideas,” said Nothstine. “I would strongly encourage younger folks that have potential to enroll in ASPLI, to help mold them in the right direction.”
Further topics covered at the institute were packaging, project management and new technology, as well as hiring, climate change, fisheries management and economic value of Alaska seafood.
“We’ll be recruiting next spring for the institute that will begin in fall 2019,” said Sannito.
Funding for ASPLI is from fees from participating companies, University of Alaska Technical Vocational Education Program funds, Alaska Sea Grant and CFOS. More than two dozen companies have paid to send employees to the institute since it began.